Work safety violations continue to be a major concern for businesses across all industries. It is a top priority for any business to avoid safety violations, but year after year, companies continue to struggle with compliance.
The Occupational Safety and Health Administration (OSHA) releases an annual list of the most common work safety violations, highlighting key areas where businesses fall short. Understanding these violations is crucial—not just to avoid fines but to protect workers and create a safer, more productive environment.
To improve compliance and create a safer work environment, it’s essential to understand OSHA’s most common work safety violations in 2024 and how to address them effectively. With more than 800 citations issued for some of the top violations, let’s dive into the biggest safety pitfalls of 2024 and how your company can stay ahead.
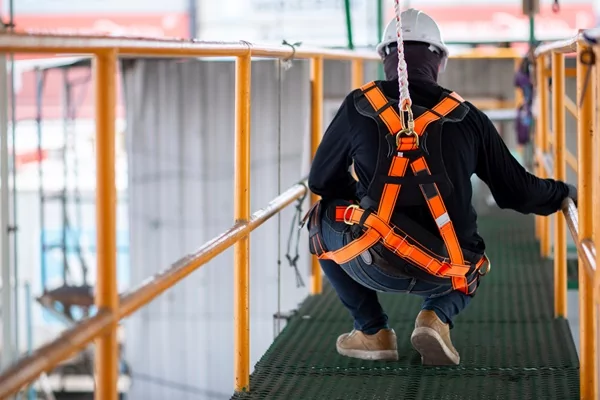
The Top 10 OSHA Work Safety Violations in 2024
1. Fall Protection (1926.501)
For the 13th year in a row, fall protection tops OSHA’s list. Falls remain one of the leading causes of workplace injuries and fatalities, particularly in construction and roofing. Common violations include failing to provide guardrails, safety nets, or personal fall arrest systems.
How to Stay Compliant:
- Conduct regular inspections of fall protection equipment.
- Train employees on proper use and maintenance of fall protection systems.
- Develop a fall protection plan tailored to your worksite.
2. Hazard Communication (1910.1200)
Many workplaces handle hazardous chemicals, yet a significant number fail to comply with proper labelling, safety data sheets, and employee training.
How to Stay Compliant:
- Ensure all hazardous materials are correctly labeled.
- Maintain up-to-date safety data sheets.
- Provide comprehensive training on handling hazardous substances.
3. Ladders (1926.1053)
Ladder-related violations are a persistent problem, with many incidents resulting from damaged or improperly used ladders. Overreaching and failing to secure ladders are also common issues.
What You Can Do:
Ladder-related violations are a persistent problem, with many incidents resulting from damaged or improperly used ladders. Overreaching and failing to secure ladders are also common issues.
- Inspect ladders before each use and remove damaged ones from service.
- Train employees on safe ladder practices, including proper setup and climbing techniques.
- Consider using alternative equipment, such as scaffolding or lifts, when appropriate.
4. Scaffolding (1926.451)
Scaffolding violations often involve inadequate platform construction, missing guardrails, and failure to inspect scaffolding before use. These oversights can lead to catastrophic accidents.
What You Can Do:
- Ensure scaffolding is erected by qualified personnel.
- Conduct daily inspections before use.
- Train employees on safe scaffolding practices.
5. Powered Industrial Trucks (1910.178)
Forklifts and other powered industrial trucks are essential in many workplaces, but they also pose significant risks if not operated safely. Common violations include lack of operator training and failure to inspect equipment.
What You Can Do:
- Ensure all operators are trained and certified.
- Conduct pre-shift inspections of powered industrial trucks.
- Enforce safe operating practices, such as speed limits and load capacity guidelines.
6. Lockout/Tagout (1910.147)
Lockout/Tagout (LOTO) procedures are designed to protect workers from the unexpected startup of machinery during maintenance. Violations often involve inadequate training and failure to implement a LOTO program.
What You Can Do:
- Develop a comprehensive LOTO program tailored to your equipment.
- Train employees on LOTO procedures and enforce compliance.
- Regularly audit your LOTO practices to identify gaps.
7. Respiratory Protection (1910.134)
Respiratory protection violations often stem from inadequate fit-testing, lack of medical evaluations, and failure to maintain respirators. These oversights can expose workers to harmful airborne contaminants.
What You Can Do:
- Conduct fit-testing for all employees required to wear respirators.
- Provide medical evaluations to ensure employees can safely use respirators.
- Regularly inspect and maintain respiratory equipment.
8. Fall Protection Training (1926.503)
While fall protection equipment is critical, training is equally important. Many violations involve failing to provide adequate training on fall hazards and protection methods.
What You Can Do:
- Provide comprehensive fall protection training for all at-risk employees.
- Document all training sessions and ensure employees understand the material.
- Regularly refresh training to keep safety top of mind.
9. Personal Protective and Lifesaving Equipment (1926.100)
PPE violations often involve failing to provide appropriate equipment or ensuring it’s used correctly. This includes hard hats, gloves, eye protection, and lifesaving equipment like life jackets.
What You Can Do:
- Assess workplace hazards and provide appropriate PPE.
- Train employees on the proper use and maintenance of PPE.
- Regularly inspect PPE to ensure it’s in good condition.
10. Machine Guarding (1910.212)
Moving machine parts can cause severe injuries, yet many workplaces still fail to install proper guards. Violations often involve missing or inadequate guards and lack of employee training.
What You Can Do:
- Install guards on all hazardous machine parts.
- Train employees on the importance of machine guarding.
- Regularly inspect machinery to ensure guards are in place and functioning properly.
The Financial and Human Cost of Work Safety Violations
Failing to adhere to OSHA standards not only results in hefty fines but can also have devastating consequences for employees.
Workplace injuries can lead to costly medical bills, lost productivity, and decreased employee morale. A strong commitment to safety not only keeps employees protected but also benefits the company’s bottom line.
Safety isn’t just about compliance—it’s about creating a culture where employees feel secure and valued. By making workplace safety a priority, companies can foster an environment where workers are more engaged, productive, and motivated.
How EHS Software Can Improve Compliance
Using an Environmental, Health, and Safety (EHS) software solution can help businesses streamline compliance efforts. EHS software simplifies incident reporting, safety training management, and compliance tracking.
Kianda EHSwise offers a customizable EHS software solution designed to help businesses improve workplace safety and meet OSHA regulations with ease.
Work safety violations can be prevented with proactive planning and proper training. By implementing strong safety programs, businesses can ensure compliance, protect employees, and enhance productivity.
Are you ready to take workplace safety to the next level? Contact Kianda EHSwise today to learn how our EHS software can help your business stay compliant and improve safety management.